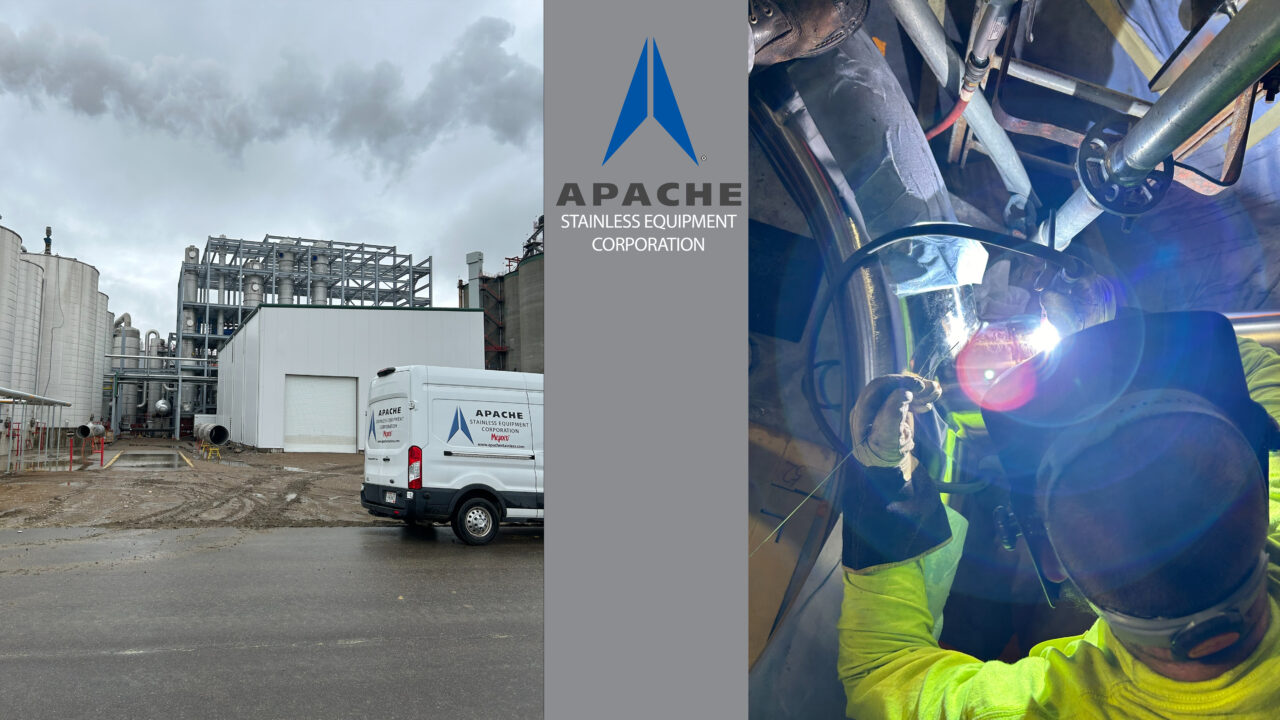
Ethanol producers have company-mandated maintenance schedules for all their production and storage vessels. When following the best prescribed maintenance processes, downtime related to repair is minimal, and the vessel’s longevity increases. When repair is needed, it is essential to ensure high-quality and efficient repair to get production back online as soon as possible.
Josh Schladweiler, field service tech and service manager at Apache Stainless, talks about repairing and modifying large ethanol process vessels and tanks. “For stainless specialty production vessels, Shell and Tube Heat Exchangers, Columns, Pressure Vessels, and Storage Tanks, we see the need for repair often caused by poor water quality, improper maintenance, wrong vessel material used for a product, or sometimes there is a process change requiring vessel modifications.”
Shell and Tube Heat Exchangers
Shell and Tube Heat Exchangers have standard maintenance protocols, including maintaining gaskets, seals, pressure relief valves, and inspection for corrosion or fatigue. The best practice for ethanol producers’ maintenance process is to inspect the shell for corrosion, cracks, and leaks and clean and inspect tubes. Ethanol Producers often have insurance mandates for these inspections. Tube deterioration risks the ethanol production process, safety, and investment.
“Tube replacement is a significant repair,” says Josh Schladweiler, “Labor, equipment costs, materials, and downtime can really add up. Annual tube inspections are highly recommended to help realize and reduce tube failures.”
Poor-quality water or unbalanced additives are common causes of tube deterioration and corrosion. After repair, stamped pressurized vessels will require new ASME documentation and an R-stamp.
Columns
Maintenance technicians should inspect trays and packing for fouling or wear in columns. As with all processing vessels, corrosion and leak checks are also part of regular equipment maintenance audits. If a repair is needed, depending on the size and repair location, it is common for columns and other processing vessels to require confined space OSHA procedures. This procedure requires a retrieval plan for one person or limited entry, ventilation, environmental oxygen monitors, and a preplanned scope of work.
Other Pressure Vessels
Pressure vessels require the same maintenance audit as other vessels, but technicians must maintain the pressure relief valves to ensure they function correctly. Ensure moving parts, such as valves and actuators, operate properly when needed.
ASME safety standards require R-stamp certified technicians to make ASME Pressure Vessel weld repairs. Repairing pressure boundaries, including the tank shell and heating and cooling jackets, will require R-stamp certification. Repairs in non-pressure areas, such as piping and fittings, may not require R-stamp certification.
Pressure vessel alterations are often due to process changes or improved technology. Repairing or altering pressure vessels require strict welding standards and procedures to maintain their integrity. Altered pressure vessels require ASME verification tests, documentation, and an R-stamp alteration class.
Maintenance or service technicians perform hydrostatic tests for leaks to verify repair or alteration, and nondestructive testing (NDT) to ensure the vessel meets safety standards. Ultrasonic (UT) tests detect internal flaws or weaknesses in the vessel wall and expansion joints. Technicians use radiographic testing to check weld integrity.
For the safest and longest use of the custom stainless vessel, regularly replace seals and gaskets, conduct maintenance audits on equipment, or consult with experienced vessel service technicians to aid in training and inspection, and determine the most proactive and efficient repairs for ethanol processing and storage vessels.
Contact Field Services if you have questions about tank maintenance.